The common defects, found in the welding part of band saw, are categorized into 4 different types which are point defect, line defect, interface defect, and bulk defect. There are varying factors contributing to the sources of defection, including these following,
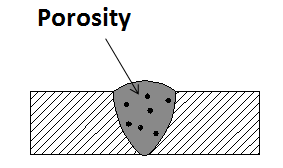
1. Porosity:
The defection starts with the occurrence of oxygen which inevitably occupies the space. During the welding process, the oxygen is restricted and unable to move out of the welding area. Resultantly, the air bubbles form once the joint has been cooled down. The porosity could occur in a particular spot or scatter around the steel. Furthermore, it takes multiple forms, including circular, cylindrical, etc.
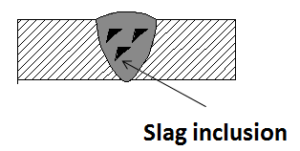
2. Slag Inclusion:
These substances could prevent the accomplishment of the band saw and also, negatively impacts the strength of the band saw which results to the band saw being fragile.
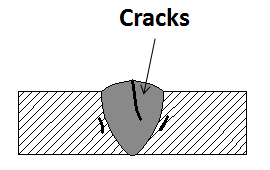
3. Cracks:
The tiny cracks on the welding joint commonly resulted from the unacceptable quality of the welding process. The quality of the welding process significantly influences the certain substances in the steel, particularly, the component of fragility. Hence, the cracks on the band saw could form and expand during the usage.
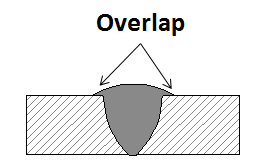
4. Overlap:
Overlap describes the situation where the band saws are not set in its right position where one edge is placed slightly on top another before entering the process of welding. This conduct results in unbalance of the band saw and could increase the risk of crack.
Bibliography :